A Badge of Honor & Duty: From Past to Present
Smith & Warren has been making badges since 1925. Their inventory exceeds 10,000 due to the longevity of the business. Every badge made may be recreated whether it was made in recent years or decades prior. Known for their high quality badges, their motto, “Built with care. Worn with Pride” encompasses the process and the relationship they maintain with their customers.
Headquartered and manufactured in White Plains, New York, Smith & Warren badges are made through a unique process relying on people for their craftsmanship. In regard to machines, they use a combination of a more traditional process and laser cut technology bringing the past and the present together to form a strong production of badges. Every piece of equipment is chosen for accuracy and quality. “We do most of the critical work in the factory by hand,” says Josh Medeiros, Director of Marketing for Smith & Warren.
“But,” he adds, “we may employ many key pieces of machinery that enable us to differentiate our badges from many other suppliers.” They use hydraulic presses to strike blanks from raw strip stock brass using steel dies. Computer engraving machines enable the engraving of lettering, ranks, etc onto badges identically—every time.
The badges start out as sheets of brass and go through a machine that stamps out the particular shape the badge will be. The rough cut is then put into a punch press to clean it up a little. Details such as the department name, rank and other information are engraved on the badge by an engraver that is computerized. Once complete, silver solder is placed to hold the backings of the badge such as the pinjoint. These areas and the back of the badge are then heated with a torch reaching roughly 1,400 degrees Fahrenheit (800 degrees Celsius), fusing the solder to the badge.
Next, a steel press is used on the badge and a mixture of water and glass beads, known as “wet blasting,” is sprayed onto the badge for a clean and more textured look.
Then, it’s time to add the details and color to the badge. This is done by hand using enamel made by gloss and water - a very old technique of metal craft. Following that, the badge is placed in a kiln allowing the gloss to adhere and harden to the badge. The badge is then rubbed up against stone in order to remove excess glass and reveal the letters and other details. After the badge is polished it is dipped into an electro-plating solution with the purpose of giving the metal added protection. The remainder of the process includes adding other touches of details such as medallions and ensuring the badge is ready to go.
“Our people are the most important component of badge making,” says Mederios. “That old school / brick and mortar approach has been and is at the heart of what we do.” But, for the more intricate designs a traditional die cutter cannot do, Smith & Warren has invested in cutting edge technology in production, such as 3D designing, prototyping, and use of high powered laser die cutting for many of custom badge orders. “It has allowed us to elevate our capability to create truly unique badge designs unlike anything anyone else is capable of,” says Mederios.
The badge is not simply a piece of attire; it is a symbol of honor and duty. Those who wear the badge want the best representation possible for their agency. Having a well-made badge, assembled with care, creativity, and professionalism, enhances that pride and honor.
The technology and skilled care that go into making Smith & Warren badges is a strong combination that produces high quality products. It’s a history like this where generations of police and other first responder families can share in the joy and pride of the badge.
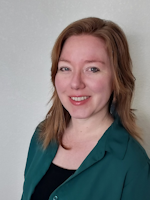
Hilary Rodela
Hilary Rodela is currently a Surveillance Officer, a former Private Investigator, a former Crime Scene Investigator, and Evidence Technician. She worked for the Ruidoso (NM) Police Department as well as the Lubbock (TX) Police Department. She has written for several public safety publications and has extensive law enforcement and forensic training and is pursuing forensic expertise in various disciplines. Hilary is a freelance public safety writer and curriculum developer for the National Investigative Training Academy.