NIJ 0101.06.
Known simply as NIJ O6, this standard establishes minimum performance requirements and test methods for the ballistic resistance of personal body armor.
The key ingredients in the NIJ 06 testing recipe are: providing adequate protection for all officers; safeguarding against a variety of ballistic threats; and designing armor that offers complete and consistent protection over its lifetime.
But this benchmark omits one key ingredient: Officer comfort. And this is a hurdle today’s body armor manufacturers have strived to overcome since the standard’s release in 2008.
“Comfort, heat and weight are all things that affect officers’ decisions to put on their vests,” says Matthew Davis, CEO of Central Lake, Mich.-based Armor Express. “We are constantly evaluating new materials and designs to make armor lighter and more comfortable without sacrifices in the ballistic protection required by the NIJ.”
Dale Taylor, COO at Diamondback Tactical of Spindale, NC, agrees. “The NIJ 06 standard is more robust than NIJ 04,” he says. “And it changed how we approached armor design. We have to meet the NIJ standard but at the end of the day the body armor still needs to be comfortable and wearable.”
Fiber manufacturers and body armor companies have met the challenges NIJ 06 presents and have kept comfort top of mind through the use of new materials, hybrid vest designs, and carrier innovations.
Less is more
When it comes to body armor, less is certainly more. The lighter the vest, the more likely it is to be worn.
Yet the 06 standard, meant to afford officers better protection, hampered manufacturer’s abilities to keep weights down.
“The changes to the standard -- the water testing, the higher velocities, the new ballistic threats, the more aggressive shot patterns, the accelerated aging -- all compounded to make for a much more aggressive standard,” says Davis. “As a result weights did increase.”
While initial NIJ 06 offerings weighed 10 to 15 percent more than earlier vests, more significant weight increases might have occurred had manufacturers such as DSM Dyneema, Dupont, Honeywell and Teijin not responded with new materials, according to Angela Milligan, director of global marketing at Diamondback.
“Suppliers like DSM Dyneema engineered new materials that resist the heat/conditioning process,” she says. “As a result, we saw a less than a five percent increase in weight.”
These new materials aided manufacturers in producing vests at weights near those possible under the previous standard. Armor Express’ The Razor vest, for instance, is constructed out of a proprietary blend of Kevlar and Dyneema and weighs .81 pounds per square foot.
“We’ve been able to remove weight pretty quickly,” says Mark Smith, vice president of sales and marketing at Point Blank Solutions Inc. of Cincinnati, Ohio. Today’s ballistic packages, he says, typically average 1-½ pounds per square foot, with some coming in at less than one pound per square foot. Point Blank’s Vision Level II concealable vest weighs just .98 pounds per square foot and is only 0.3 inches thick but it protects against 2-, 4-, 16- and 64-grain RCC bullets.
“Innovation usually catches up to anything that changes in the standard, and that’s exactly what has happened,” says Bob Weber, director of ballistic development for Safariland of Ontario, Calif. “The difference is that the lighter, midline, lightweight vests have more nonwoven products in them than they had previously.”
He explains today’s vests incorporate aramid and polyethylene nonwovens in their designs, and utilize a hybrid designs that enable manufacturers to achieve lighter weights and greater flexibility. “I sometimes have three to four materials in a single product,” he says.
Manufacturers like Safariland are also adding materials such as Unequal’s DEFCON technology, a trauma sports material found in helmets and umpire vests, in order to keep weights down. This composite material enables Safariland to produce vests thin and flexible vests. The proprietary formulation absorbs and dissipates more energy per square inch than traditional trauma products and reduces more blunt force trauma in one panel than several layers of ballistic materials combined, notes Weber.
Manufacturers also see nanoparticle technology as a possible means to an end. Most bullet-resistant vests utilize multiple layers of Kevlar, Twaron or Dyneema fibers to stop bullets from penetrating by spreading the bullet’s force over a larger area. Even with this protection, wearers may still be left with blunt force trauma. The elasticity of nanotechnology’s carbon nanotubes may enable manufacturers to reduce blunt force trauma without increasing vest weights.
“We are looking at advancements in nanoparticle technology, which absorbs and distributes energy and seems to have some utility in bullet-resistant vest design,” says Weber.
Some like it wet
“When you get bullet-resistant materials wet, it renders them ineffective. The weave opens up and expands and puts holes or gaps in the material,” says Melissa Allerman, vice president of Sonobond Ultrasonics of West Chester, Penn.
This fact is the impetuous behind the NIJ 06 testing protocol, which requires body armor test panels to be dunked in water for 30 minutes before shot testing.
“Armor manufacturers are now using ultrasonic welding to meet this requirement,” says Taylor.
Ultrasonic welding seals the ballistic panel edges without stitching to prevent water and moisture from seeping in and degrading their ballistic integrity.
But it’s not to be confused with heat-sealing, says Allerman, who points out that ultrasonic welding is a completely different process.
“Heat sealing exposes an outside heat source to the material, but ultrasonic welding generates very little heat,” she explains. “It coverts electrical energy into mechanical energy when it passes through piezoelectric crystals under compression.”
Sonobond teamed with nylon manufacturers producing materials for ballistic panel outer-coverings to add a low-melt urethane coating to one side of the nylon. This coating allows manufacturers to ultrasonically weld these coverings. Currently Brookwood Companies Inc. produces the nylon used in Sonobond’s ultrasonic welding process.
Sonobond’s SeamMaster ultrasonic welding system cleanly cuts and seals the nylon’s edges in one pass. “The ultrasonic horn transmits energy to the material,” Allerman says. “It vibrates at 20,000 times a second, and excites the molecules in the thermoplastics to seal the edges.”
While Brookwood isn’t the only manufacturer of such materials, it produces the only nylon that works with Sonobond’s technology, which is utilized by most body armor manufacturers, according to Allerman.
Taylor agrees. “Not all sonic weldable materials are created equal,” he explains. “Some are quite hard and make a crinkling noise. We were able to work with suppliers to come up with one that could be sonic welded but was a soft, pliable fabric as opposed to a rigid and stiff material.”
“We were already seam-sealing before the NIJ 06 standard came out,” adds Davis. “We switched to a new cover made by Brookwood that is ultrasonically welded. And we worked very closely with Sonobond to make sure the seams were incredibly strong.”
Threat assessment
The Golden Rule when it comes to body armor is that it should protect officers from the threat of their own bullet.
Line-of-duty deaths increased 13 percent in 2011, with 173 officers losing their lives. Sixty-eight of those officers died in firearms-related incidents and four of them died from shots fired from their own guns.
The bullet officers carry should serve as a baseline for body armor protection, says Taylor, who then recommends agencies catalogue and monitor the threats they are removing from the street and make sure their body armor covers those threats as well.
“This gives you an idea of what’s in your area,” he says. “California is going to have different special threats than Miami and New York is going to have different threats than both of them. It depends on what’s readily available.”
Manufacturers constantly adapt their designs to what Weber calls the “bullet flavor of the month.” “There are always newer and faster bullets on the market,” he explains.
Taylor agrees noting in years past a 9mm round was a 9mm round, but as projectile technology and composites change, manufacturers have adapted their bullet-resistant offerings.
“We now have projectiles in some calibers with velocities in excess of 2,000 feet per second from a hand gun,” Taylor says. “With the introduction of these new high-speed rounds, it’s important for end-users to know that armor is bullet resistant not bullet proof. With the emergence of high-speed threats, there are additions that must be added because soft armor only gives so much performance. You don’t have to go to a rifle plate Level III or IV, but you can put some thin, lightweight plates inside the trauma plate pocket in the carrier.”
Enter Bourque Industries. This company manufactures tactical plates made out of Kryron, a carbon nanotube metal matrix composite manufactured from standard alloys and base metals. This hard armor withstands multiple high-velocity impacts in the same location, performs consistently across the entire surface of the armor plate even for half-on/half-off edge shots, and eliminates ricochet and spall, according to John Bourque, CEO of the Tucson, Ariz. firm.
“With Kryron the first round shock hardens the material, allowing for multiple impacts,” Bourque says. “Most ceramic products massively fracture upon impact. Our plates allow for multiple impacts without fragmentation or spall being ejected from the front of the plate.”
The plates also dissipate heat coming from the projectile itself. “When people get shot with a bullet there is enormous heat trapped in the plate and it can burn your body,” Bourque explains. “Our product eliminates that heat from those rounds, including phosphorous rounds.”
Bourque plates weigh less than 1½ pounds and have been engineered to fit comfortably across the torso. “The biggest complaint we heard about hard plates was that the curve typically rested on their rib cages and if they hit the ground, it was very uncomfortable,” Bourque explains. “They wanted something that fit closer to the body and that’s what we provided.”
Keeping it cool
Officers often forgo wearing their vests when it’s hot outside. But there are a number of developments helping to keep wearer’s cool when they don this protection.
Carriers designed to be worn outside the uniform shirt lift body armor away from the body to help keep officers cool. These carriers can either look like a uniform shirt with ballistic protection inside or have a tactical look and feel with the vest noticeable to others.
Either way, they keep officers cooler than body armor worn tight against the skin. “Instead of having it on inside their shirt, against their body, it’s worn on the outside where they can loosen it up and get more air underneath,” Taylor says.
The look an agency ultimately selects comes down to personal preference, adds Tim O’Brien, category director-concealable armor, Safariland. “Some agencies want a uniform look so they choose a uniform carrier that looks just like the vest itself,” says O’Brien. “Others want a load-bearing vest that allows them to place equipment on the vest and take some of the weight off the duty belt.”
However, Davis says he strongly believes vests worn on the outside need a “chameleon effect.” He explains when a suspect shoots an officer he typically aims for center mass. But when that suspect can readily see an officer’s bullet-resistant vest, he may aim for the head instead.
“An external carrier that’s designed to look like a uniform shirt provides better concealability through a chameleon affect,” Davis emphasizes.
On the horizon, officers may soon don vests equipped with built-in cooling systems.
Empa, working with Unico Swisstex, has prototyped a Kevlar vest with a built-in cooling system consisting of coolpads filled with water and a miniature fan that blows air through a fabric spacer behind the pads to cool the vest and the person wearing it.
“The fans had to be extremely small with very low power consumption and an air stream designed to provide good ventilation,” explains Empa researcher Markus Weder.
The coolpads also required tweaking. “The original coolpad membrane, when filled with water, could cool for about an hour,” Weder explains. “But for law enforcement, that timeframe was too short. We put a flexible bottle into the vest that can be filled with water to lengthen cooling time to three hours.”
The new vest has been tested by Zurich City police officers who have reported that it offers a great deal of cooling efficiency, according to Weder.
Unico plans to bring the vests to market by year’s end. “Unico will feed a small number of vests into the market and when they get feedback from the marketplace, they have planned a wider release,” Weder says.
NIJ 06 may have been a game changer when it comes to body armor design, but it wasn’t a game stopper. As manufacturers continue to create body armor that meets the new standard, they have kept a trained eye on the wearer himself.
“If the vests aren’t comfortable, officers won’t wear them, and then they are not doing their job,” says Milligan. “We want to build armor that officers want to wear and is comfortable so they wear it and it saves lives.”
HEADLINE: NIJ 06 requirements
With NIJ 06 in place, body armor manufacturers must meet more stringent requirements than ever before, including:
-- Increased test velocities for IIA, II and IIIA vests.
-- A submersion test requiring test panels to be fully immersed in 70-degree water for 30 minutes prior to shot testing. (Prior standards only required a water spray test for six minutes.)
-- An accelerated aging test that includes extensive environmental conditioning, including a requirement that panels be tumbled for 72,000 cycles over a 10-day period at 149 degrees Fahrenheit and 80 percent humidity.
-- A more aggressive shot pattern.
-- An increase in the number of shots under which the vest must perform reliably. The number of shots is nearly 90 percent more than required previously.
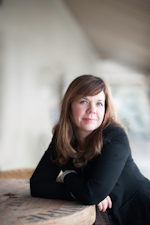
Ronnie Wendt | Owner/Writer, In Good Company Communications
Ronnie Wendt is a freelance writer based in Waukesha, Wis. She has written about law enforcement and security since 1995.